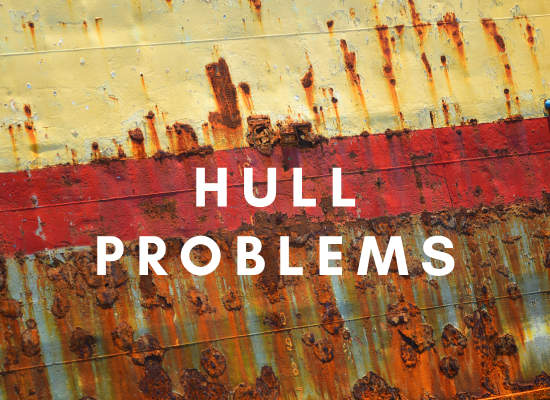
The construction of ship hulls primarily uses materials chosen for their strength, durability, and resistance to harsh marine environments. The most common material is steel, favored for its robustness and cost-effectiveness. Steel hulls are prevalent in older cargo ships due to their ability to withstand heavy loads and rough conditions. Aluminum, lighter than steel, is sometimes used in superstructures to reduce overall weight, but less frequently in hulls due to its higher cost and lower resistance to abrasion.
Other materials such as fiberglass and wood are generally reserved for smaller vessels and not typically relevant for large, ocean-going cargo ships over 30 years old. Innovations in material technology like high-tensile steel offer greater strength and corrosion resistance, but these may not be found in ships constructed three decades ago unless retrofitted.
Impact of Design and Material Choices on Hull Longevity
The longevity and susceptibility to damage of a ship’s hull are directly influenced by the design and materials used. Steel, while strong, is particularly prone to corrosion (rust) when not properly maintained with coatings and cathodic protection. The design of the hull also plays a crucial role; for instance, sharper bows are more efficient at cutting through water but may experience more stress, leading to potential structural issues.
Compartmentalization within the hull can affect its survival capability in the event of flooding, while the thickness and grade of the material used can determine how well the hull withstands pressure and impact damage. Additionally, older designs might not have accounted for modern loading conditions or the use of heavier, modern containers, which can stress the hull structure beyond its original capacity.
Signs of Hull Deterioration
Visual Signs of Deterioration
The most apparent signs of hull deterioration in older cargo ships include:
- Rust and Corrosion: Look for brownish stains or flaky metal on the hull’s surface, a clear sign of iron oxidizing. This is common in areas where protective coatings have failed or are absent.
- Deformation: Buckling or bending of the hull plates can occur under physical stress or from hitting docks and floating debris. These deformations weaken the structural integrity of the ship.
- Paint and Coating Failure: Bubbling, blistering, or peeling of paint can expose the underlying metal to elements, accelerating corrosion.
Less Obvious Signs of Deterioration
Some signs of hull deterioration are not immediately visible but are critical to identify:
- Hairline Fractures: These small cracks in the hull can be hard to spot without close inspection but can grow under the stress of regular use, leading to significant damage.
- Electrolytic Corrosion: This type of corrosion occurs when different metals in electrical contact are submerged in an electrolyte (seawater). It can cause rapid material degradation but may not be noticeable without electrical potential testing or detailed inspections of areas typically hidden from view, like bilges and under machinery.
Corrosion Assessment
Types of Corrosion Affecting Ship Hulls
Corrosion is a primary concern for the integrity of any metal structure, including ship hulls. Understanding the different types of corrosion can help in identifying potential weak spots and preventing catastrophic failures:
- Galvanic Corrosion: Occurs when two different metals are in electrical contact in a conductive solution (seawater). The more anodic metal will corrode faster than it would alone, while the cathodic metal will corrode slower. For instance, if a steel hull is in contact with a copper-based alloy, the steel will deteriorate.
- Pitting Corrosion: This type of corrosion leads to the formation of small holes in the metal. Pitting is especially dangerous because it can be hard to detect and can penetrate deep into the metal, causing severe structural damage over time.
- Crevice Corrosion: Develops in confined spaces where seawater gets trapped. These areas can be under gaskets, washers, or bolt heads, and once initiated, crevice corrosion can lead to rapid deterioration of the metal within the confined space.
Techniques for Assessing Corrosion
To accurately assess the extent of corrosion and its impact on hull integrity, several techniques are employed:
- Visual Inspection: The most straightforward method, involving thorough checks for signs of corrosion. Special attention is paid to known problem areas such as weld joints, bilges, and fittings.
- Thickness Gauging: Ultrasonic thickness gauges are used to measure the thickness of the hull’s metal, comparing it against the original thickness to determine how much material has been lost due to corrosion.
- Electrochemical Testing: Methods like potentiodynamic polarization can help in assessing the corrosion potential of the hull materials in their operational environment, providing insights into corrosion rates and preventative measures.
Structural Integrity Tests
Non-Destructive Testing Methods
Ensuring the structural integrity of an aging ship’s hull involves various non-destructive testing (NDT) methods, allowing for detailed inspections without causing any damage to the ship:
- Ultrasonic Testing (UT): Uses high-frequency sound waves to detect flaws in the metal structure. UT is particularly useful for finding internal defects that are not visible to the naked eye.
- Radiographic Testing (RT): Involves the use of X-rays or gamma rays to view the internal structure of welded joints and other critical areas. This method provides a photographic record of the condition and can show cracks, voids, or inclusions in metals.
- Magnetic Particle Inspection (MPI): Used primarily to detect surface and slightly subsurface discontinuities in ferromagnetic materials. MPI can reveal cracks, seams, and other imperfections.
Use of Drones and ROVs for Underwater Inspection
Technological advancements have enabled more thorough inspections of ship hulls through the use of drones and remotely operated vehicles (ROVs):
- Drones: Aerial drones equipped with high-resolution cameras can inspect above-water sections of the hull and hard-to-reach areas, providing real-time video feed and photographs to inspectors.
- ROVs: These are particularly useful for underwater inspections, allowing for a close examination of the hull below the waterline without the need for dry-docking the ship. ROVs can be equipped with various sensors and tools to measure thickness, detect metal stress, and even perform minor repairs.
Common Areas of Concern
Prone Areas in Aging Ship Hulls
Certain areas of a ship’s hull are more susceptible to damage over time, especially in vessels over 30 years old. Understanding these common areas of concern helps in prioritizing inspections and maintenance:
- Keel: The keel bears much of the structural load and is fundamental to the ship’s stability and structural integrity. Damage or weakness in this area can be catastrophic.
- Bilge Areas: These are low points where water tends to collect, making them hotspots for corrosion and rust.
- Ballast Tanks: Often subject to varying levels of water and air, which promotes corrosion. These tanks are crucial for the ship’s balance and stability, making their integrity vital.
- Deck Plates and Bulkheads: Repeated stress, poor maintenance, and exposure to harsh environmental conditions can lead to degradation over time.
Tips for Focused Inspections
To effectively monitor these critical areas, the following strategies can be employed:
- Regular Scheduled Inspections: Establish a routine schedule to inspect these areas thoroughly, using appropriate testing methods discussed earlier like ultrasonic testing and visual assessments.
- Priority to High-Risk Areas: Always give higher priority to areas known for rapid deterioration such as the bilge and ballast tanks.
- Detailed Documentation and Reporting: Keep detailed records of all inspections, including photographs and descriptions of any changes or deterioration over time. This helps in tracking the progression of damage and planning maintenance.
Impact of Fouling and Marine Growth
How Biological Growth Affects Hull Integrity
Marine organisms like barnacles, algae, and mussels can adhere to the hull and multiply, leading to biofouling. This accumulation can significantly affect the ship’s performance and structural integrity:
- Increased Drag and Fuel Consumption: Heavy fouling increases drag, reducing speed and significantly increasing fuel consumption.
- Hull Corrosion: Some types of fouling can accelerate the corrosion process. For instance, the acidic byproducts from certain organisms can degrade protective coatings and directly corrode the metal.
- Blockages and Damage: Growth in crucial areas like cooling intakes and around sensors can lead to operational failures.
Methods for Assessing and Cleaning Marine Growth
Maintaining a clean hull is essential for the safety and efficiency of the vessel:
- Regular Dry Docking: Ships should be dry-docked at regular intervals recommended by regulatory bodies and classification societies to clean and inspect the hull thoroughly.
- In-Water Surveys and Cleaning: If dry docking is not feasible, underwater ROVs and divers can be employed to perform in-water surveys and cleaning. This method is cost-effective and less disruptive.
- Anti-Fouling Coatings: Applying or reapplying anti-fouling coatings can prevent the growth of marine organisms. These coatings are designed to be smooth and toxic to certain marine life, reducing the likelihood of attachment.
Repair Techniques for Aged Hulls
Common Repair Techniques
Repairing the hull of an aged cargo ship involves several sophisticated techniques that can restore structural integrity and extend the vessel’s operational life:
- Welding: The most common method for repairing steel hulls, welding can fix cracks, strengthen weakened areas, and replace corroded sections. Special care must be taken to match the welding material to the existing hull material to avoid introducing stresses that could lead to further damage.
- Cladding: This technique involves adding a new layer of material over existing metal surfaces. It’s particularly useful for addressing extensive corrosion and wear. Cladding can restore the surface integrity of the hull and protect against future corrosion.
- Epoxy Fillers: Used for smaller repairs, particularly in dealing with pitting corrosion. Epoxy fillers can be used to fill pits and small holes effectively, restoring surface continuity and preventing further ingress of water.
Choosing Between Repair and Replacement
Deciding whether to repair a damaged section of the hull or replace it entirely depends on several factors:
- Extent of Damage: If the damage is widespread or involves critical structural areas, replacing the entire section may be more cost-effective and safer in the long run.
- Cost Considerations: Although replacement can be more expensive upfront, it may offer better longevity and less maintenance down the line compared to repeated repairs.
- Operational Downtime: Consider how each option impacts operational downtime. Repairs might be quicker but less durable, while replacement could mean more time in dry dock but fewer future disruptions.
9. Regulatory Compliance and Documentation
Maritime Regulations Concerning Hull Integrity
Maintaining hull integrity is not just a matter of safety and efficiency but also of legal compliance. Various international and national bodies set regulations that must be adhered to:
- International Maritime Organization (IMO) Standards: The IMO issues global standards, including those related to the structure and maintenance of ship hulls. These are enforced through inspections and certifications.
- Classification Societies: Bodies like Lloyd’s Register, American Bureau of Shipping, and others provide specific guidelines and certificates for hull integrity, often dictating the repair methods and materials that can be used.
Importance of Documentation
Keeping thorough documentation is crucial for several reasons:
- Legal and Regulatory Compliance: Documentation proves compliance with maritime laws and regulations. Inspection reports, repair logs, and certificates must be current and accessible for audits.
- Operational History: Detailed records help identify recurring issues or patterns of wear that can inform future maintenance and repair decisions.
- Resale Value: Comprehensive and well-maintained logs can enhance the ship’s resale value, providing potential buyers with proof of diligent maintenance and compliance with safety standards.
Summary of Key Points on Assessing Hull-Related Issues
Assessing the hull integrity of used cargo ships over 30 years old is a critical aspect of ensuring their safety, efficiency, and compliance with maritime regulations. Key areas to focus on include:
- Material and Design: Understanding the materials used in the hull’s construction and the design’s impact on its longevity.
- Signs of Deterioration: Regularly inspecting for visual and structural signs of deterioration such as corrosion, deformation, and hidden fractures.
- Corrosion Assessment: Identifying different types of corrosion and employing various techniques to assess their severity.
- Structural Integrity Tests: Using non-destructive testing methods like ultrasonic testing, radiographic testing, and employing drones and ROVs for comprehensive inspections.
- Common Areas of Concern: Paying special attention to areas prone to damage such as the keel, bilge areas, and ballast tanks.
- Marine Growth Impact: Managing fouling and understanding its effects on hull integrity and ship performance.
- Repair Techniques: Deciding between repairing and replacing damaged sections based on the extent of damage, cost considerations, and operational downtime.
- Compliance and Documentation: Adhering to maritime regulations and maintaining thorough documentation to ensure compliance and enhance the ship’s operational history and resale value.
Guidelines for Making an Informed Purchase Decision
When considering the purchase of a used cargo ship that is more than 30 years old, prospective buyers should follow these guidelines to make an informed decision:
- Comprehensive Pre-Purchase Inspection: Engage with maritime surveyors or inspection services to conduct a detailed evaluation of the ship, particularly the hull’s condition.
- Review of Documentation: Examine all available documentation, including repair logs, previous survey reports, and compliance certificates, to gauge the ship’s maintenance history and regulatory compliance.
- Assessment of Repair and Maintenance Costs: Estimate the immediate and future costs of necessary repairs and ongoing maintenance. Consider the total cost of ownership, including potential increases in operational costs due to aged infrastructure.
- Consultation with Experts: Seek advice from naval architects, marine engineers, and classification societies to understand the technical and regulatory implications of any observed hull issues.
- Risk Evaluation: Evaluate the risks associated with the age and condition of the ship, including potential downtime and the feasibility of obtaining insurance coverage.
- Long-Term Viability: Consider the ship’s suitability for your specific needs and its long-term viability given current maritime industry trends and environmental regulations.